- 27 maart 2024
- Door ir. Koen Faes (BIL), ir. Rafael Nunes (BIL), ir. Jean Lamontanara (MA srl, Gruppo CLN) & ir. Pietro Perlo (Interactive Fully Electrical Vehicles)
Realtime kwaliteitsmonitoring van lasprocessen
Een grote zorg bij lassen is om lasdefecten snel, betrouwbaar en kostenefficiënt op te sporen. De huidige destructieve en niet-destructieve technieken zijn tijdrovend en duur en zijn niet altijd geschikt om de laskwaliteit te beoordelen. Met real-time kwaliteitscontrolesystemen kunnen de huidige beperkingen van conventionele beproevingstechnieken worden overwonnen. In het Europese project AVANGARD werd dit onderzocht voor het lassen van een innovatief chassis voor elektrische voertuigen.
Context
Lassen is een van de meest gebruikte fabricageprocessen. Het wordt voor bijna alle metaalproducten gebruikt. Inherent aan fusielasprocessen worden er echter defecten gegenereerd bij de fabricage van metaalproducten als gevolg van de complexiteit van het lasproces. De aanwezigheid van defecten resulteert in een stijging van de productiekost, verspilling van productietijd, energie of grondstoffen (schroot, of nood aan herstellingen), vertragingen in de levering en gevolgen voor de veiligheid.
Voor een productiebedrijf is het daarom van belang om defecten zo snel mogelijk op te sporen, bij voorkeur al tijdens het productieproces, om snel in te grijpen en te voorkomen dat nog meer producten gebreken vertonen of dat deze producten verder worden verwerkt.
Laskwaliteit
Het opsporen van imperfecties wordt in de huidige industriële praktijk uitgevoerd aan de hand van manuele, offline methoden. Hierbij wordt vaak een combinatie van oppervlakteonderzoek (bv. visueel, penetrant of magnetisch) en volumetrisch onderzoek (bv. ultrasoon of radiografisch) toegepast.
Samengevat zijn deze technieken tijdrovend, gefocust op een beperkte set imperfecties, kunnen ze geen in-line, real-time uitspraak doen over de kwaliteit en zijn ze niet in staat de volledige productie-output te verifiëren. Soms is inspectie zelfs onmogelijk. Zo kunnen hoeklassen niet op een niet-destructieve manier worden geïnspecteerd op inwendige lasfouten.
Destructieve proeven worden selectief uitgevoerd, wat betekent dat een selectie van producten wordt getest. Dit alles gebeurt na de productie, wat ook betekent dat de verdere verwerking van het product wordt stopgezet totdat de resultaten van de testen bekend zijn. Dit alles leidt tot een verhoging van de kostprijs van de producten.
Real-time kwaliteitscontrole
Als alternatief voor de bovengenoemde methoden, stijgt de interesse voor real-time in-line monitoringstechnieken, die niet alleen het manueel aspect vermijden (arbeidsintensief), maar eveneens toelaten de volledige productie-output te beoordelen. Hierbij wordt de kwaliteit van de lassen onmiddellijk na of zelfs tijdens de productie gecontroleerd. Dit maakt het mogelijk om de kosten voor kwaliteitsinspectie te verminderen, aangezien er in internationale normen een tendens bestaat om een vermindering van het niet-destructief onderzoek toe te laten, indien controle via elektronische methoden consistent een aanvaardbare kwaliteit aantoont.
Real-time kwaliteitsmonitoring maakt het ook mogelijk eerder in te grijpen bij producten met gebreken, waardoor het verlies aan energie, grondstoffen en productieafval sterk wordt beperkt, met als einddoel een productie zonder gebreken.
Adaptieve regeling van lasprocessen
In een later stadium kunnen gesloten-regelsystemen gebruikt worden, met corrigerende maatregelen tijdens het lassen, en zo de 'first time right'-productie mogelijk te maken. Er wordt hierbij gewerkt met een procesbesturingssysteem dat veranderingen van de lasomstandigheden detecteert met behulp van sensoren en toelaat om in real time de lasparameters aan te passen.
Toepassing van artificiële intelligentie
Sensoren genereren grote hoeveelheden data die op een snelle en effectieve manier moeten verwerkt worden. Intelligente softwareoplossingen kunnen de grote hoeveelheden data die door een lasproces worden gegenereerd, analyseren om trends en patronen te identificeren, die vervolgens gebruikt kunnen worden om lasfouten te detecteren en om de lasprocessen bij te sturen of efficiënter te maken.
Artificiële Intelligentie-methoden vertonen het verrassende vermogen om niet-lineaire correlaties en interactie-effecten met groot succes te detecteren. Wegens de complexiteit van het lasproces en de vele interfererende factoren, worden AI-methoden steeds vaker door onderzoekers gebruikt om de output van een lasproces te voorspellen.
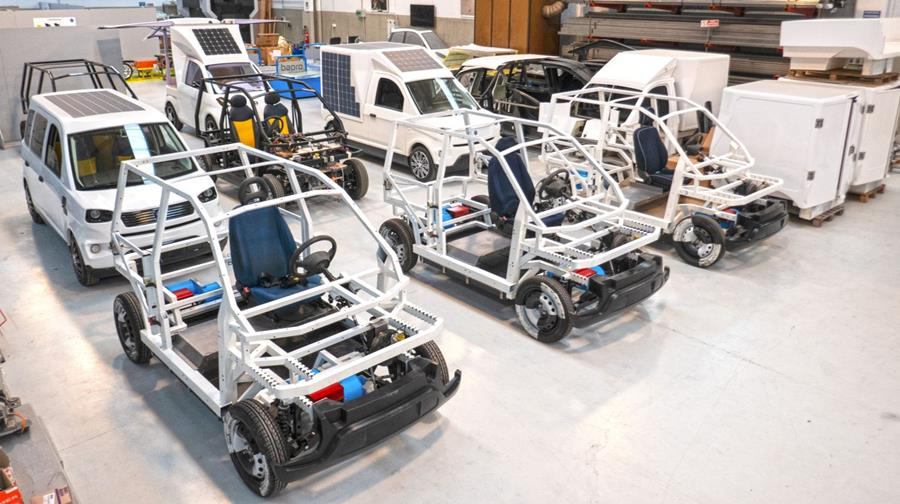
Meettechnieken
In de afgelopen decennia zijn er veel nieuwe meetmethodes op de markt verschenen die belangrijke informatie opleveren over de kwaliteit van lasverbindingen en gelaste producten. Zo bestaan er verschillende soorten sensoren om real-time bewaking van het lasproces uit te voeren; zoals boogsensoren, optische, ultrasone en infraroodsensoren. Aangezien elk monitoringsysteem voor- en nadelen heeft, is de juiste keuze van de te gebruiken techniek niet altijd makkelijk. De belangrijkste bewakingssystemen die voor lastoepassingen gebruikt kunnen worden, worden hierna kort besproken.
Boogsensoren
Boogsensoren monitoren de booglengte. Wanneer de positie van de elektrode ten opzichte van het werkstuk verandert, kan een TIG-lastoorts, uitgerust met een servomechanisme, het signaal van een boogsensor gebruiken om de positie van de elektrode ten opzichte van het werkstuk aan te passen, zodat de gemeten spanning gelijk is aan de gewenste referentiespanning.
Optische sensoren
Visie-gebaseerde systemen worden gebruikt om de conditie van het smeltbad te bepalen. Het gebruik van normale camera's maakt het mogelijk een lasproces in real time te visualiseren en kan gebruikt worden voor de controle van defecten aan het oppervlak, zoals spatvorming, randinkarteling en uitlijningsfouten van de lasnaad. Een hogesnelheidscamera kan tot 250.000 beelden per seconde filmen en kan gebruikt worden om snelle veranderingen in het proces te detecteren, zoals variaties van het lasbad (vorm, grootte …), het inbrengen van het toevoegmateriaal in het lasbad en zelfs de frequentie van het loskomen van de druppels gesmolten metaal.
Infraroodcamera's en sensoren
Infraroodsensoren detecteren de infraroodstraling uitgezonden door een materiaal. Daarom worden deze sensoren gebruikt voor lasprocessen, die thermische processen zijn, om het proces te bewaken en te monitoren. Deze sensoren meten de emissie aan het oppervlak van de las en geven informatie over de afkoelsnelheid, de lasbreedte en penetratiediepte. Ze kunnen ook gebruikt worden voor lasnaadvolgsystemen. Infrarood thermografie (IRT) is relatief nieuw voor lasinspectie. IRT-methoden zijn contactloos, waardoor ze geschikt zijn voor in-line detectie.
In het AVANGARD-project heeft het B.I.L. deze monitoringstechniek onderzocht voor het bewaken van de laskwaliteit van hoeknaden. Speciale software werd gebruikt die een aantal tools bevat om de beelden van de lascamera automatisch te verwerken en om te detecteren of er iets misgaat tijdens de lascyclus. Door toevoeging van kleur aan een monochroom beeld kunnen specifieke kenmerken in dit beeld gezien worden die anders niet zichtbaar zouden zijn. Figuur 1 toont hoe verschillende kenmerken van het originele beeld (figuur 1, links) makkelijker te zien zijn wanneer pseudokleuring wordt toegepast (figuur 1, rechts). Kenmerken zoals de oppervlaktestructuur van het basismateriaal, het helderste deel van de lasboog en het smeltbad kunnen worden verbeterd met pseudokleuring.
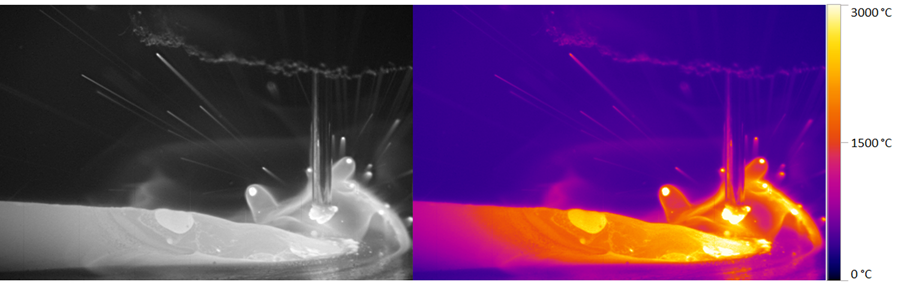
De 'Blob Analysis'-tool in de software is een krachtige machine vision tool die een verscheidenheid aan eigenschappen kan meten in een bepaald gebied, zoals de temperatuur, grootte, vorm en locatie van het smeltbad (figuur 2).
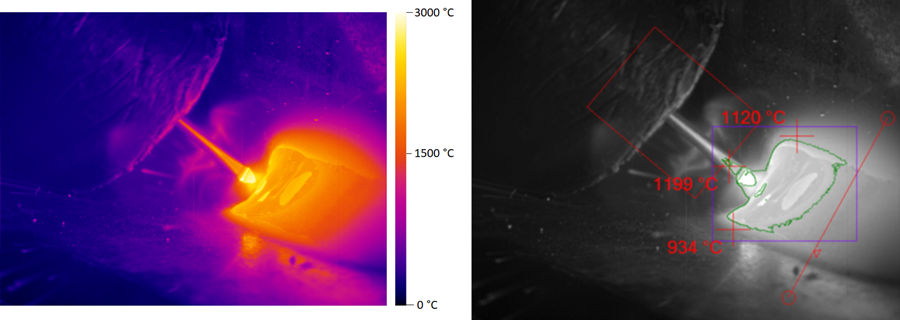
Figuur 2: temperatuurmetingen via een thermische camera (bron: BIL)
Met het hulpmiddel 'Edge Locator' kan een randdetectie en -analyse uitgevoerd worden om randen of gebieden met snelle contrastverandering op te sporen (figuur 3).

Het uiteindelijke doel is om via machine vision tools de beelden van de las te verwerken, automatisch informatie te laten extraheren en op basis van deze gegevens feedback te leveren aan een processturing (closed loop-regeling). Met de juiste machine vision tools zouden fabrikanten hun lasprocessen volledig automatisch kunnen maken, zodat operatoren niet hoeven in te grijpen tijdens het lassen. De combinatie van infraroodlascamera's en machine vision tools kan dit mogelijk maken.
Ultrasone sensoren
Ultrasone sensoren meten de akoestische emissie tijdens het lassen (figuur 4). Dit zijn hoogfrequente geluidsgolven, die geproduceerd worden tijdens of kort na het lassen. Akoestische-emissiemonitoring (AEM) kan uitgevoerd worden tijdens alle karakteristieke fasen van het lasproces: tijdens het lasproces zelf, onmiddellijk na het lassen en tijdens de levensduur van de las.
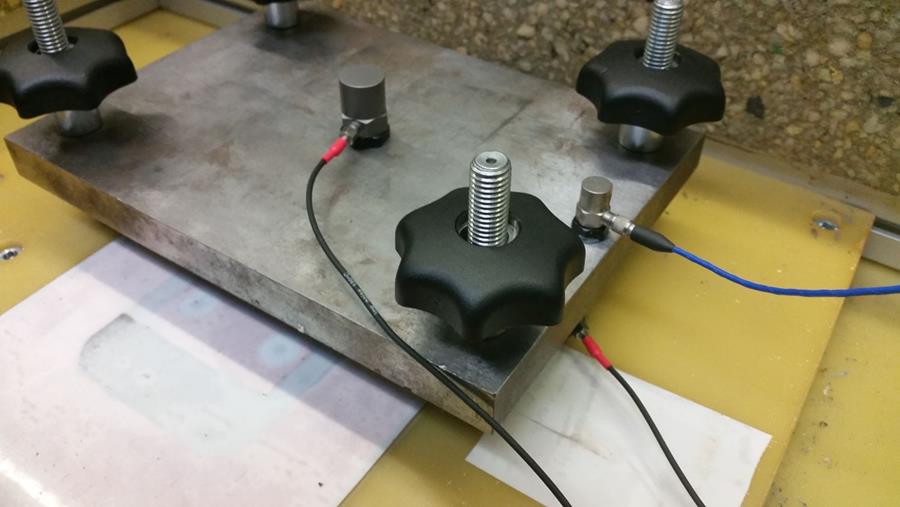
Figuur 4: AEM toegepast voor het elektromagnetisch pulslassen (bron: BIL)
Tijdens het AVANGARD-project werden experimenten uitgevoerd voor het monitoren van het gerobotiseerd MIG/MAG-lassen op basis van akoestische emissie (figuur 5). Datagedreven AI-modellen werden gebruikt om de laskwaliteit te voorspellen en om optredende onvolkomenheden te herkennen en classificeren. Voor het gerobotiseerd MIG/MAG-lassen van hoeknaden werden de akoestische emissiemetingen gekoppeld aan de types lasonvolkomenheden, gedefinieerd volgens ISO 5817. Aan de hand van het waargenomen akoestische spectrum kon een uitspraak gedaan worden over het type lasonvolkomenheid en de locatie in de las. Met de AI-modellen was het ook mogelijk om te voorspellen of een bepaalde lasonvolkomenheid acceptabel was of niet volgens ISO 5817.
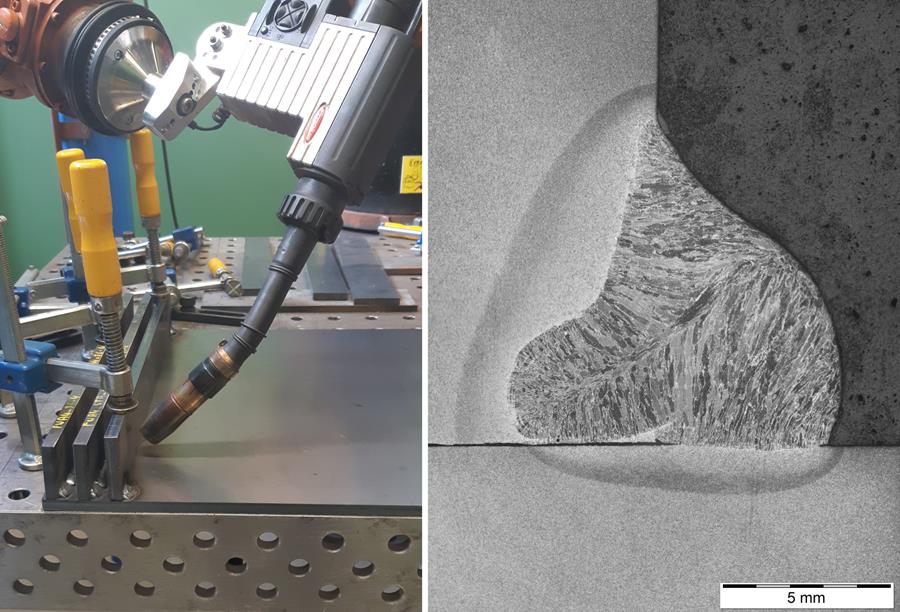
Figuur 5: links: opstelling voor akoestische-emissiemonitoring van MIG/MAG -
rechts: voorbeeld van een las met defecten (bron: BIL)
Spectroscopie
Een spectrometer meet de intensiteit van een lichtstraal bij verschillende golflengten. Veranderingen in de frequentie-inhoud kunnen geanalyseerd en in verband gebracht worden met de procescondities of -storingen.
Laserscanners
Een laserscanner meet de geometrie van lasverbindingen. Algoritmen berekenen vervolgens de oppervlaktekenmerken van de las. De implementatie van analysesoftware maakt het mogelijk om grotere secties van de verbindingen in veel minder tijd op te meten en te documenteren dan bestaande analoge meettechnieken. Het systeem zorgt voor een herhaalbare methode die onafhankelijk is van de operator, die snel is en de mogelijkheid heeft om de volledige lasgeometrie continu vast te leggen met een hoge resolutie (figuur 6). Het Belgisch Instituut voor Lastechniek (BIL) beschikt over een laserscanner die momenteel gebruikt wordt in een aantal onderzoeksprojecten.
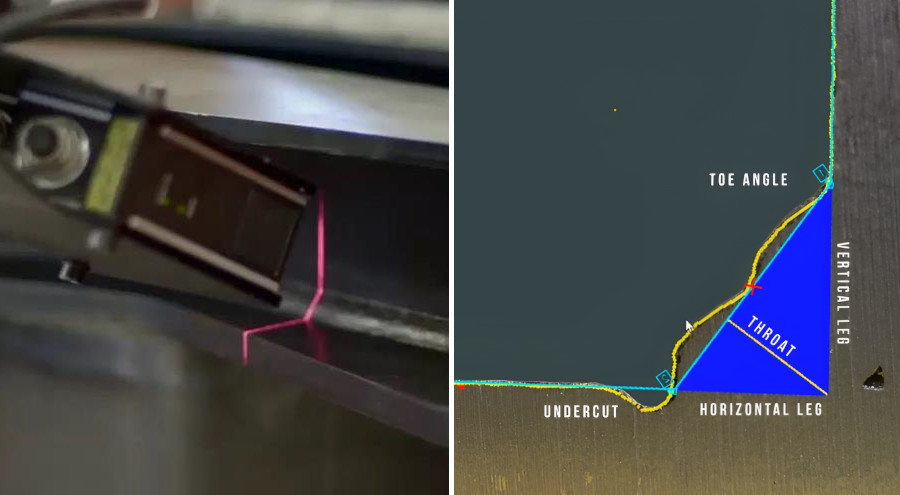
OPROEP TOT DEELNAME AAN EEN NIEUW PROJECT
Het Belgisch Instituut voor Lastechniek zal verder onderzoek uitvoeren om de bruikbaarheid te onderzoeken van kwaliteitscontrole van lasverbindingen met behulp van systemen voor in-line, real-time detectie van lasfouten tijdens het lassen.
De voordelen van dergelijke systemen zijn:
• vroegtijdige opsporing van defecten,
• vermindering van productiekosten, verlies van productietijd, energie of materiaal, vertragingen bij de levering en gevolgen voor de veiligheid,
• mogelijkheid om 100% van de lasnaden te testen,
• vermindering van het aantal destructieve en niet-destructieve offline testen,
• volledige traceerbaarheid van het product,
• hogere betrouwbaarheid van vervaardigde producten,
• gesloten-lus-kwaliteitscontrolesystemen zijn mogelijk.
Het doel van het project is het onderzoeken van real-time kwaliteitsbewaking voor het lassen. Aspecten die hierbij onderzocht zullen worden zijn de te gebruiken meetmethoden en sensoren, en het correleren van de metingen met de laskwaliteit. Hiervoor zullen software-algoritmes ontwikkeld worden op basis van artificiële intelligentie.
Is deze ontwikkeling interessant voor u of zou deze kunnen worden toegepast op uw materialen of producten, deel dan uw visie en help ons de nieuwe ontwikkelingsmogelijkheden in kaart te brengen. U kunt contact opnemen via de website van het Belgisch Instituut voor Lastechniek (BIL) of via e-mail (Koen.Faes@BIL-IBS.be).
Dankwoord: AVANGARD wordt gesteund door het Horizon 2020 onderzoeks- en ontwikkelingsprogramma van de Europese Unie, onder het contract Nr. 869986.